Let's Talk About Screen Print Ink and How Important is to Use Quality Ink on Your Products
Quality Screen Printing
Screen printing uses heavier and thicker inks. You may ask why this is so important. Well, this thicker ink appears more vibrant when printed on your items. In addition to making your signage easier to see, rich color printing promotes your business. In addition, screen printing is able to withstand various environmental conditions and can be very reliable.
However, this is not recommended for environments where exposure to chemicals or abrasives predominates. Although some degradation will inevitably occur, a screen printed object can last for years with an excellent appearance. For indoor warning and instructional signs, screen printing is extremely useful.
Consistency of Screen Printing Ink
The quality of screen printing depends largely on the consistency of the ink. Ink can be divided into categories depending on how liquid or dense they are. Some printers try to change the angle and pressure of the squeegee to accommodate ink consistency. This will likely make screen printing much more complex, and if done by hand, it can even cause carpal tunnel syndrome or joint pain.
The Importance of Preparing Your Ink
After all, all inks require some preparation before screen printing. Even if you don't need additives to help with the effect or procedure and your ink is the right color and consistency, you still need to prep it! To keep the color and texture consistent, you should always mix ink, whether by hand or in an ink mixer. Because you find out too late that the ink isn't ready for the task, preparing the ink before it hits the screen can save you from having to stop your work to re-print or clean your stencils.
How to Improve Screen Printing Ink Quality
Using two components known as a soft hand-held clear base or filler and a curable thinner is the correct approach to change the way ink is printed. To change ink pigmentation, use a mild hand cleaner. A mild manual cleaner changes the amount of pigment in ink and also makes it creamier and easier to screen print. Soft transparent hand ink enhances screen printing quality as it requires less squeegee pressure than standard inks.
Depending on the texture of the curable thinner can be used in amounts from 2-4 to 10 percent, and it changes the sticky properties of the ink. The curable thinner facilitates ink shear, which improves print quality. Therefore, it is critical to adjust ink as needed to improve registration, save ink, and make screen printing faster and easier.
Creating a Special Effect
Preparing the ink will also allow you to create unique print effects. Several ink additives are available that change the quality of your ink. With the addition of additives, you can give your ink a plump look, a glossy finish, or a softer texture. You can use glitter or metallic powder with ink if it has a metallic base. For a suede look, a smoother can reduce the sheen of the plastisol.
You can use additional ingredients to get different results from your inks. Sometimes you may need to add a thickening paste. A flow control additive can be used if you are printing color work or halftones, as it reduces the amount of ink that sticks to the back of the screen and prevents wet-on-wet printing. You can see some models in
our catalogue!
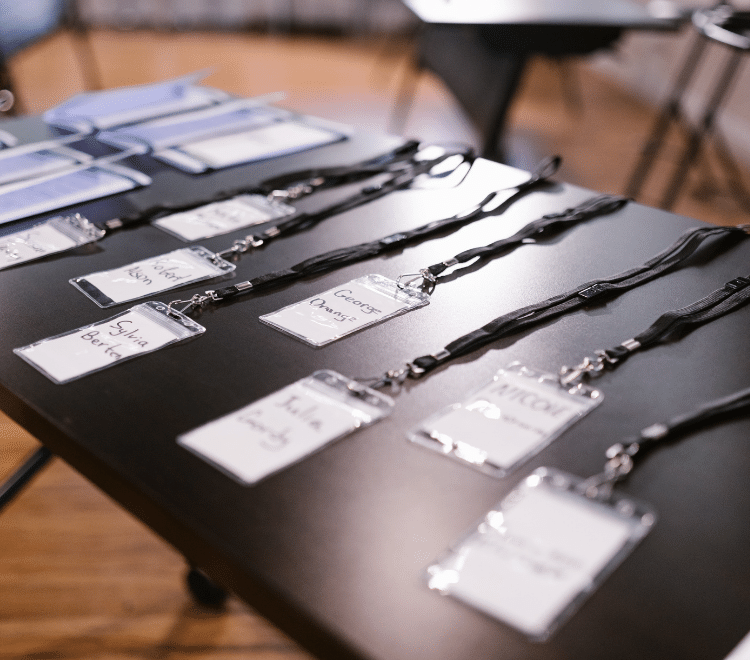